Piezoelectric MEMS Foundry Service

Our piezoelectric MEMS foundry service supports the development of high-performance piezoelectric MEMS devices using our superior single-crystal piezoelectric deposition and MEMS processing technologies.
We offer flexible services such as buffer wafer supply, and specific MEMS processing to meet your requirements.
Our Core Technologies
- KRYSTAL® Wafer manufacturing and deposition technology for single-crystallization.
- MEMS Process technology to maximize the single-crystal thin film capability.
- Main Products and Services
- The World's Leading Piezoelectric Technology
- MEMS Process Menu
- Example of Process (Deep-RIE)
- Example of Steps from Inquiry to Mass Production
Main Products and Services
Contract processing services for piezoelectric MEMS, and PZT and non-lead material high performance piezoelectric deposition services, sales of underlayers and single crystal deposition substrates, Piezoelectric MEMS design support, etc.
We offer flexible services such as buffer wafer supply, and specific MEMS processing to meet your requirements. Please feel free to contact us.
The World's Leading Piezoelectric Technology
By combining the plasma control technology cultivated through DLC deposition and inorganic crystal control technology, we have succeeded in single-crystallization of various piezoelectric materials, which were considered extremely difficult to produce, and established manufacturing methods.
It can be adapted to various semiconductor processes and exhibits significantly higher properties than existing polycrystalline materials.
MEMS Process Menu

-
Process Wafer Sizes: 6 & 8 inch
-
Cleanliness: PZT Deposition Class 100 (Other Class 1000)
Process Type | Process | Processing Equipment |
Deposition | Piezoelectric Thin Film (PZT) | RF Magnetron Sputtering, Sol-gel |
Metal Oxide (SRO) | RF Magnetron Sputtering | |
Metal Oxide (ZrO2) | Evaporation | |
Metal Film (Au, Pt, Ti, Cr*) | DC Magnetron Sputtering | |
TEOS-SiO2 | PE-CVD | |
Al Deposition* | RF Magnetron Sputtering | |
Photolithography | Resist Coating / Developing | Spin Equipment |
Exposure | Double-sided Mask Aligner | |
(Front-back, IR Transmission Alignment) | ||
Cleaning | Resist Stripping Cleaning | Dip Washing |
O2 Ashing | ICP-RIE, CCP-RIE | |
Etching | Dry Etching (Au, Pt, Ti, Cr*) | ICP-RIE |
Dry Etching (PZT) | ICP-RIE | |
Dry Etching (SiO2) | ICP-RIE | |
Si Deep RIE | Deep-RIE | |
(Top-to-Bottom through-hole processing) | ||
Wet Etching (PZT, Au, Ti) | Spin Etch Can be dipped) | |
Temporary Bonding | Adhesive Bonding | Heat and Pressure |
Evaluation | - | Optical Microscope, |
Laser Microscope | ||
SEM / EDX | ||
XRD | ||
XRF | ||
Piezoelectric Properties Evaluation System | ||
Stress Measurement | ||
Resistance Measurement Film Thickness Measurement |
||
Others (Partners) |
Dicing | Blade, Stealth |
Grinding | Grinding, Polishing | |
Thermal-SiO2 | Thermal Oxidation | |
Wafer Level Bonding | Heat and Pressure | |
Design and Analysis | Device Structure Analysis and Design | (Please contact us) |
*Need to check details of requirements when considering those processes.
We can also provide services for processes not listed in the menu above, supplied PZT wafers made by other companies, or only specific processing steps.
Please feel free to contact us.
Examples of Process:
(Some examples of MEMS devices we have processed.)
- Inkjet heads (actuators, flow paths, nozzles)
- MEMS mirrors (for automotive and consumer applications)
- Piezo MEMS microphones
- Piezo MEMS speaker
- MEMS micro pumps
- MEMS ultrasonic sensors
- MEMS smell sensors
etc.
Example of Process (Deep-RIE)
Example of silicon deep etching process by the Deep-RIE equipment
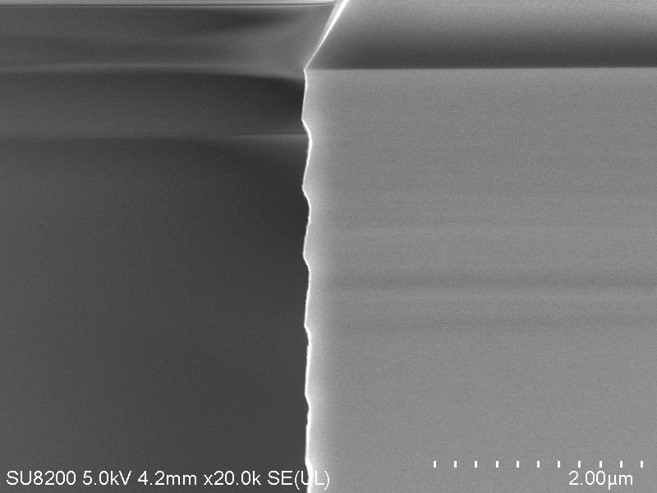
Scallop 100 nm or less (87.0 nm)
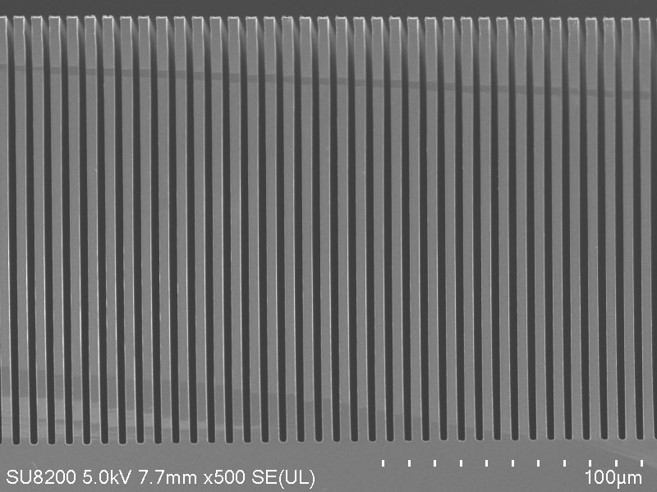
Aspect ratio of 50 or more (57.3)
*Other process are also available, such as taper shape control, through-silicon processing, plasma dicing, etc.
Example of Steps from Inquiry to Mass Production
- MEMS processing technology to maximize the performance of single-crystal piezoelectric thin films
- Flexible support for piezoelectric MEMS, from design support to processing
![]() |
• Meetings / Consultations |
• Requests | |
• Technology Introduction | |
etc. | |
![]() |
• NDA Execution |
• Specification Details | |
• Process Discussion | |
etc. | |
![]() |
• Trial Production Quotation |
• Rough Quotation for Mass Production | |
• Trial Production Agreement | |
etc. | |
![]() |
• Design Verification |
• Process Trial Production | |
• Inspection and Shipping | |
etc. | |
![]() |
• Trial Product Evaluation |
• Feedbacks on Evaluation | |
• Decision for Mass Production | |
etc. | |
![]() |
• Finalize Specifications |
• Finalize Quotation for Mass Production | |
• Mass Production Agreement | |
etc. | |
![]() |
• Ordering / FCST Information |
• Start Mass Production | |
• Feedbacks on Mass Production | |
etc. | |